At the beginning of this year, the redesigned Varimat Roofing Machines were unveiled by Leister, representing a significant leap in technology and functionality.
Leister’s research and development team collaborated closely with industry experts to address key welding requirements and rectify design shortcomings present in a large range of similar roof welding tools on the market.
The VARIMAT 700 automatic welding machine ensures consistent process reliability and precise tracking for flat roof welding tasks. With its high contact pressure, innovative nozzle swivel-in mechanism, LQS (Leister Quality System), and efficient power management, it guarantees top-notch welding quality. Additionally, integrated running lights illuminate the welding area, proving invaluable in low-light conditions.
Key features of the VARIMAT 700 include:
- Enhanced welding reliability due to increased contact pressure
- Precise tracking enabled by variable transport axis
- Quick nozzle insertion with the swivel-in mechanism
- Visual alarm alerts when deviating from the welding window
- Flexible voltage options between 230V and 400V
The VARIMAT 500 shares most features with the VARIMAT 700, except there is no LQS system on board. However, users can leverage the myLeister app to access live machine data on their smart phone or tablet for monitoring purposes.
As the entry-level model, the VARIMAT 300 offers basic functionality without data recording or monitoring capabilities. It can only be purchased in either the 230V or 400V set up. Unlike the VARIMAT 700 and VARIMAT 500, the VARIMAT 300’s internal electronics limit adaptability.
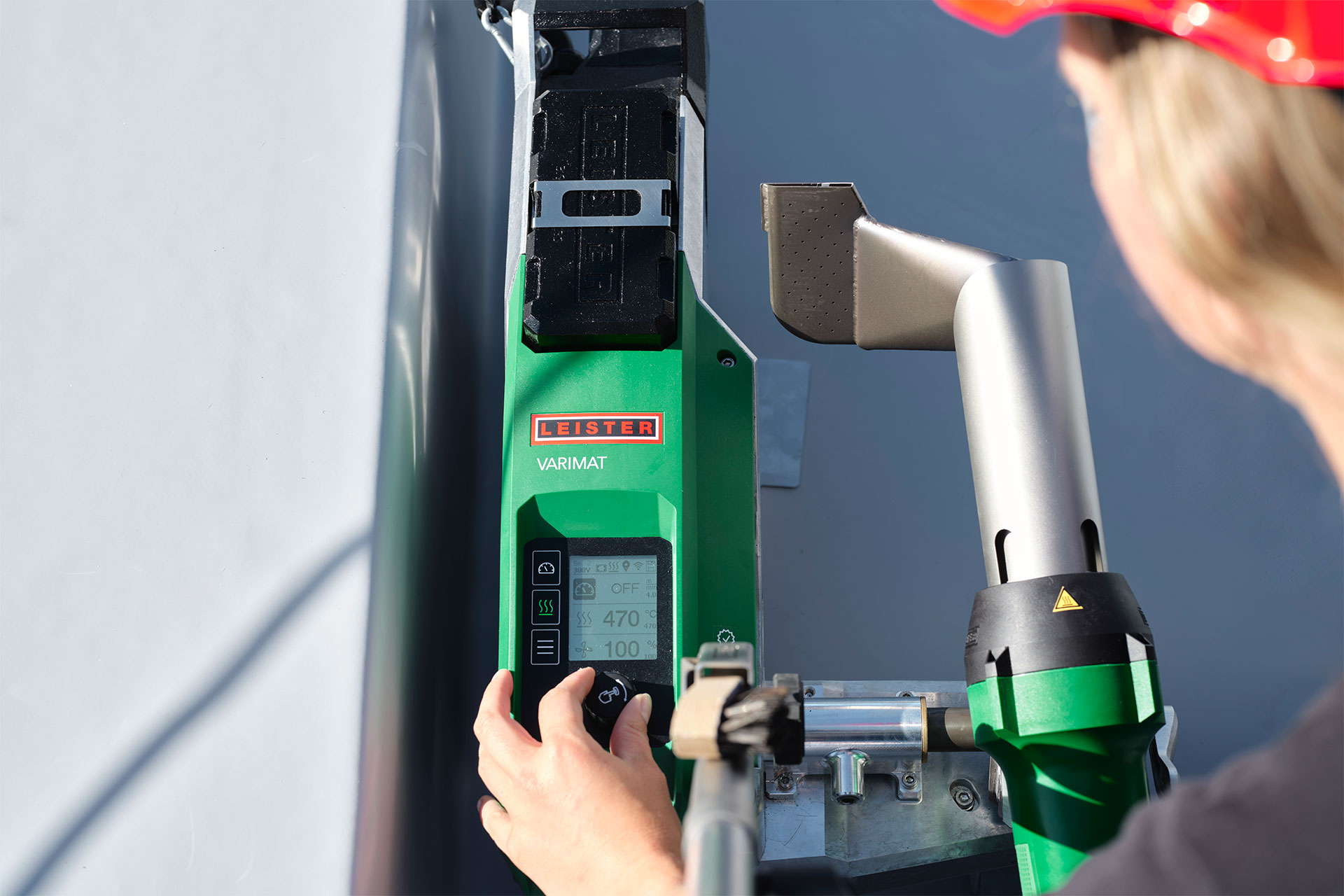
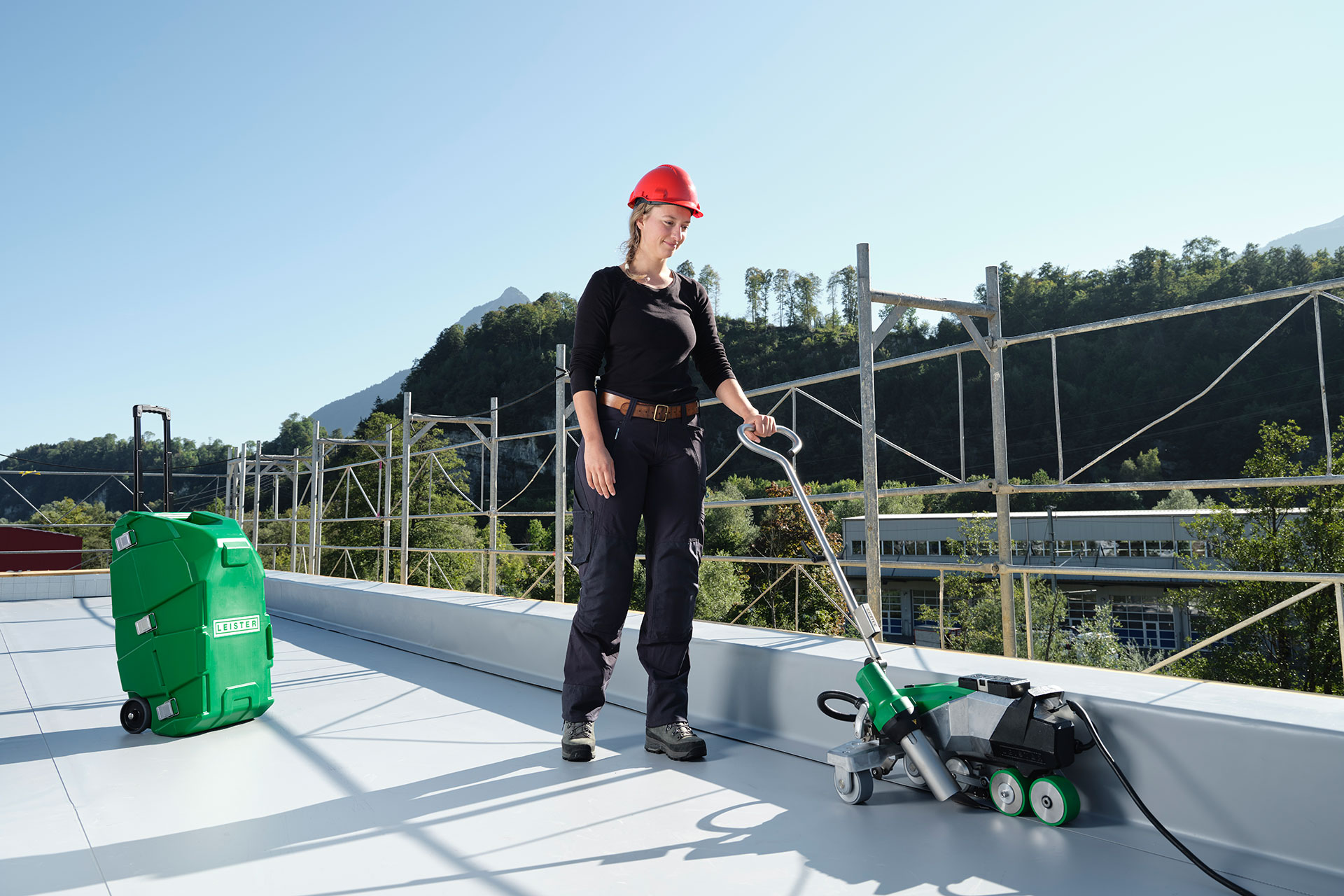